When we purchased this home in August 2013 we immediately struggled with the kitchen layout. While the previous owners had opted for a large dining set in the middle of the room, we felt like this was a cramped setup, and struggled to make the space work with a centered dining table.
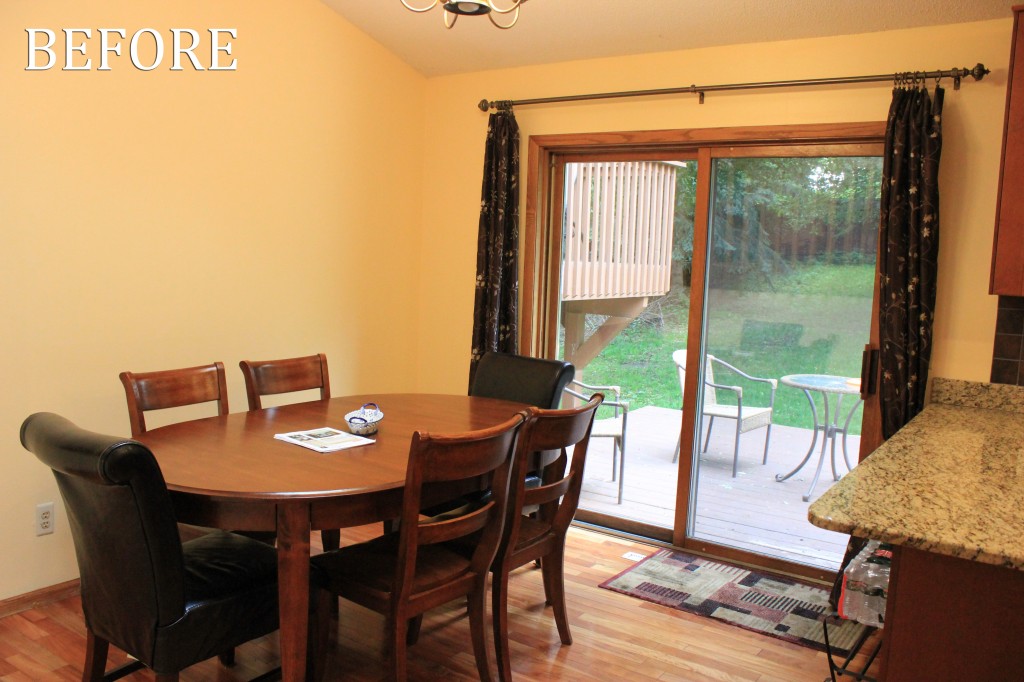
What this image doesn’t show is that when the chairs next to the wall are pulled out, to sit down at the table, they hit the wall. Chair scuffs/wall scuffs galore.
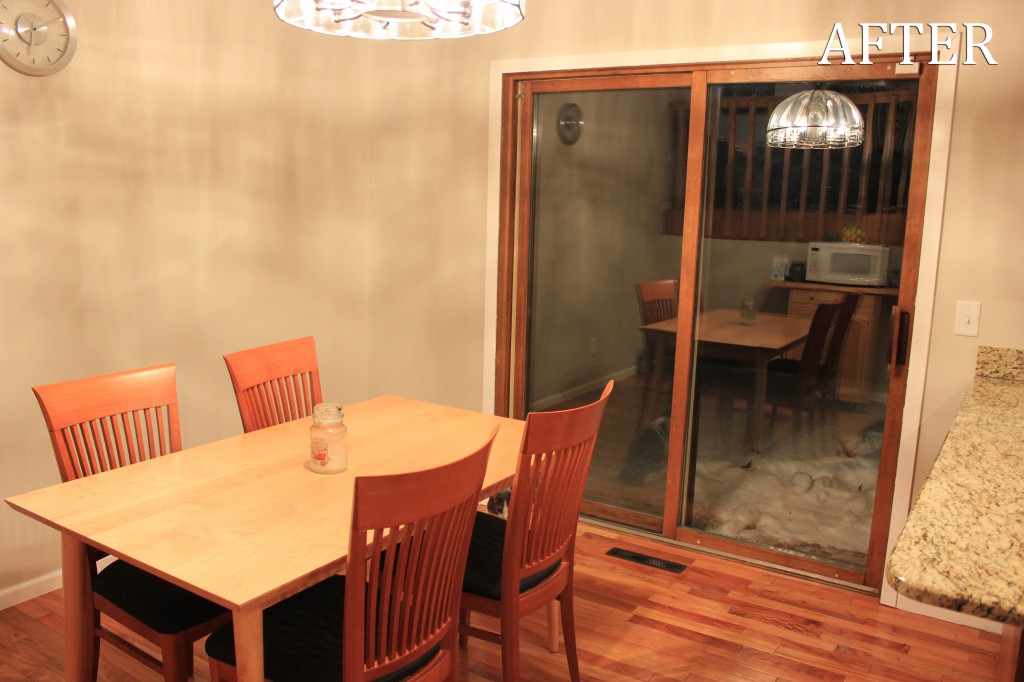
Again, not a great option, this is actually an Ikea desk that we’ve been using as a dining table since we snagged it from a friend for a great price.
So, the struggle continued, until we finally started searching for better options for the space. Finally a photo on Houzz delivered inspiration.
After assessing our space we stared the build by taking off the baseboards.
Mike then started building the frame and supports for an idea of how much of the space we wanted the banquette to take. He started by cutting 3/4″ plywood for what would become the major support structures in the banquette.
After cutting seven pieces, Mike lined them up and clamped them together. Using a belt sander, we made sure they were all the same shape.
The first segment was a bit of an experiment. We needed to find a way to use as few 2x4s as possible so that we would have as much interior storage space as possible remain for multiple kitchen uses. We also had to keep the frame sturdy enough for multiple butts and think about what would need to be attached to the seat in later steps (hinges, etc).
Here you see the skeleton of the banquette starting to take shape in the dining room.
Added 2×4 supports to connect the corners together.
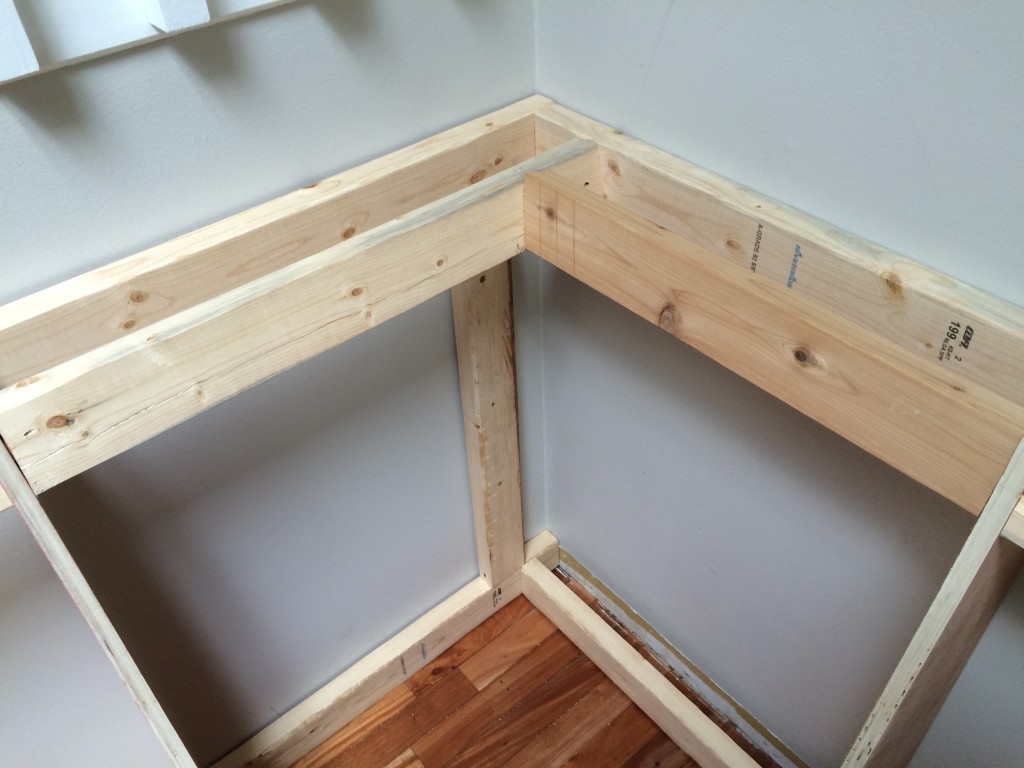
The first compound miter cut! 11 degrees one direction and 11 degrees the other direction. It’s simple over short distance like a 2×4, but wait to see the head-scratcher I was about to run into.
The corner needed angled supports for the seat backs to rest against.
OK, the next series of photos will be dealing with the technical details of how to angle a seating area into an imperfect corner. We understand if you want to jump ahead and just look at the progress photos below (I know I would).
Before you read the following details, please keep in mind that I was a “C” student in math growing up (Sara has no comment regarding her Math grades). You know how when you’re in high school math, and you joke with all you friends, “When will we ever use this information?” the answer is: after you buy a 30 year old home and decide to build a series of things that attach to the settled warped walls (except for proofs – you will never in your life need to write a Geometry proof again after 10th grade, that shit is useless). For this project, I needed to accurately calculate and mark lines to make compound miter cuts (more than one angle at one time). The biggest cut was going to be in the corner where the seat backs met together. I needed to take into consideration the angle that the seat on the left would bend back, and also the angle of the seat on the right for how the two pieces fit together. I first held an angle tool up to the bench and saw that it bent back at an angle of roughly 10.5 degrees. I marked the board using that information:
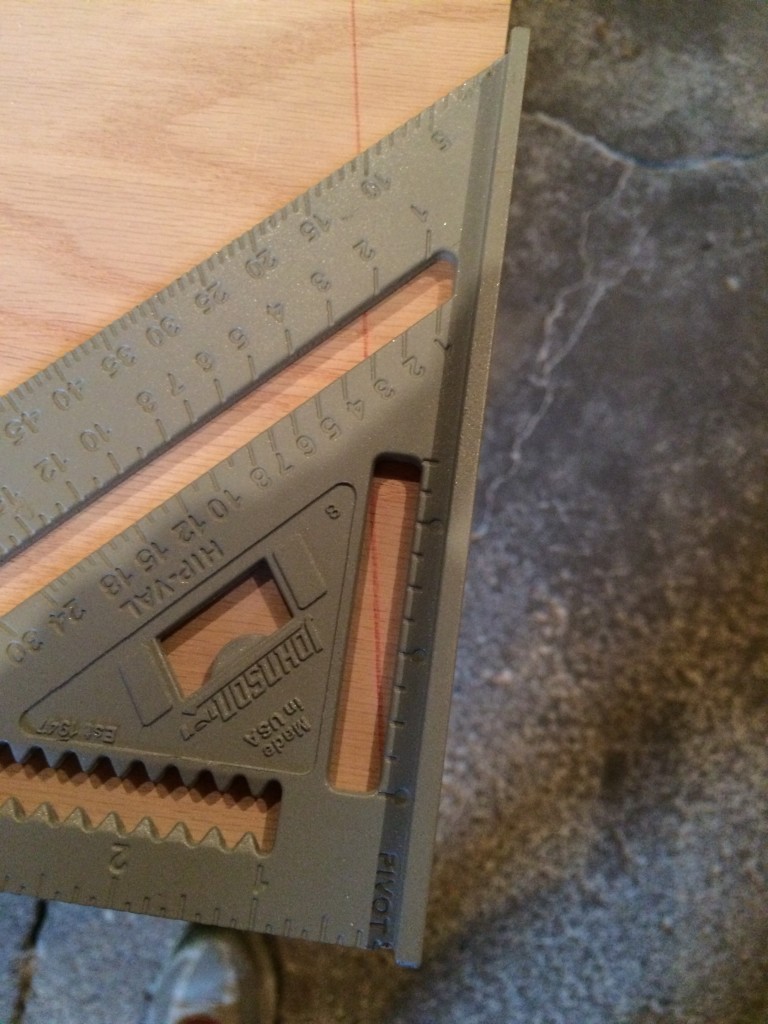
Also, these photos have been brought to you by Excedrin Migraine, “Excedrin, the headache medicine.”
The red line on the board below shows where the cut would have been made if I didn’t take time to measure a second way. Over such a large distance, I minor miscalculation could have devastating results and ruin a fairly pricey piece of oak plywood.
In the original plan, the seats bent back 11 degrees, which is why I was confused when the angle tool told me otherwise. Using a tape measure, I double checked the height and width of the boards I had already cut in the dining room. I used an online angle tool to compare the angle of 10.5 degrees I had marked with the original dimensions. Here’s what I found:
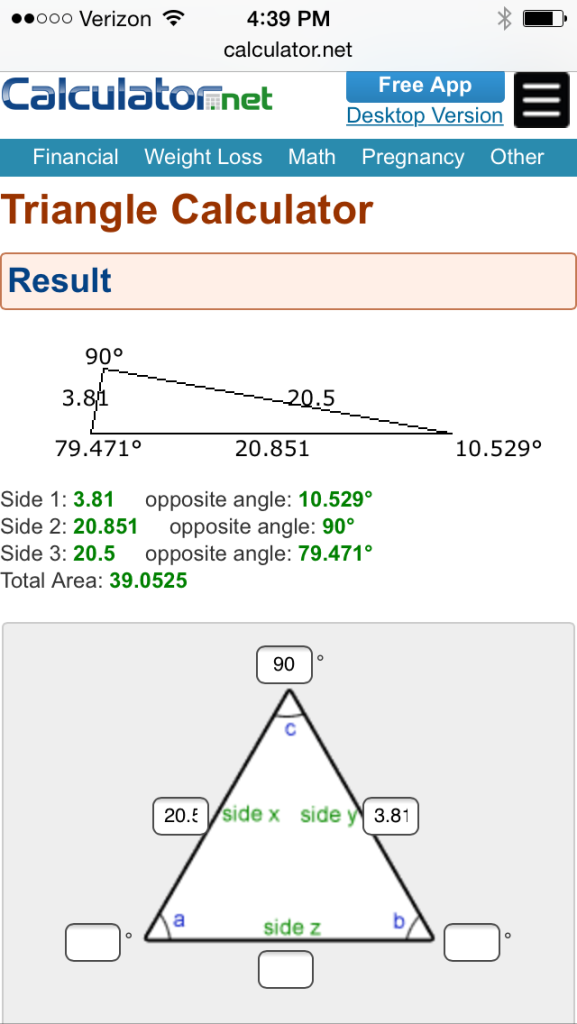
The information I entered in the bottom of this picture shows the distances I measured that would be shaved off if I continued with the 10.5 degree angle that was marked first.
There is the moment I started to scratch my head. I knew from the original plan that the area I was dealing with had a height of 20.5 inches and a depth of four inches. Measuring 3.81 after marking the 10.5% angle made me want to re-calculate with an 11 degree angle instead:
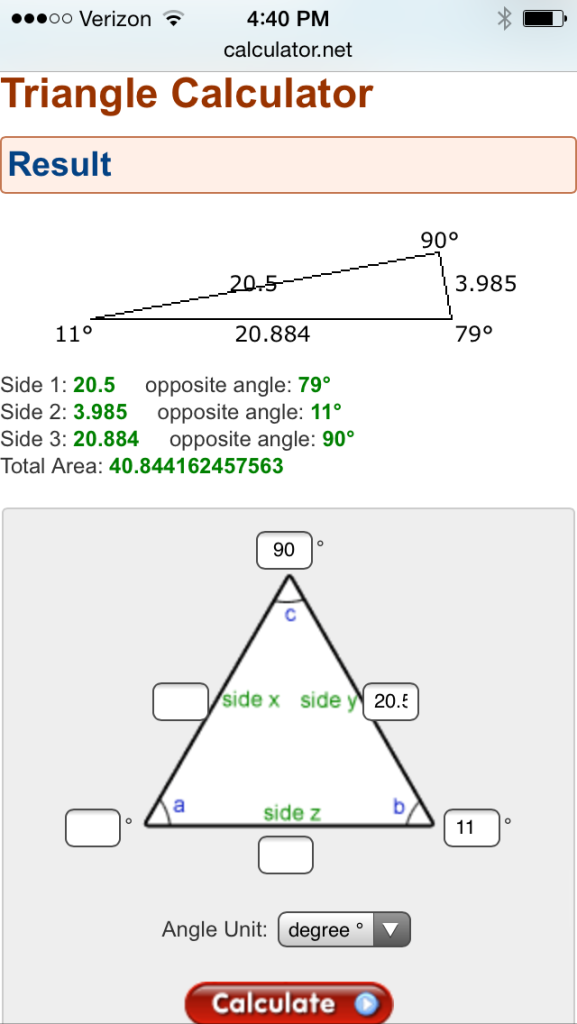
I used the calculator to input angle-side-angle. 90 degrees and a bench length of 20.5 inches, and an 11 degree angle at the top. Notice at the top of this image, the calculation that shows 3.985. This is much closer to the original dimensions of 4 inches, so I knew this had to be correct.
Using this different method of measuring the angle, I marked on the board where 3.985 would be. It was about a quarter inch away from where I marked the other cut.
After I had that angle marked, I simply adjusted my handsaw to 11 degrees and made the cuts. Then, the fun part. Piecing them together:
Once the wood for the seats was cut, it was time to start staining.
Like previous projects, we used a Cabot Black Cherry wood stain. We wanted to continue the theme of dark stain and white paint that was used in previous permanent projects in the house.
The boards were secured from beneath with 2x4s so no nails or screws would be visible from above.
I love this part, you can finally see a banquette coming together.
For the sides of the banquette, we went with a pre-finished decorative wood paneling and poplar wood for the trim. I used a router to leave space for the plywood to fit beneath the trim pieces and also to give the trim a beveled edge around the sides.
On the right side of the banquette, I installed an electrical outlet to plug in the microwave. It is essentially a glorified extension cord with a fancy face plate, with a plugin on the inside of the banquette connected to the existing wall outlet.
For the base of the banquette, we used the same decorative plywood, but went with vinyl trim pieces to give it a finished look.
Here’s what we’ve all been waiting for (this includes every friend/family member we’ve had over in the last two years that we invited to eat with us in the living room). After a few throw pillows and a new table (that’s actually a dining table and not a desk), we have a place to eat our meals and entertain guests!
Edit: Now that this is all put together, we’re seriously considering painting the entire banquette white (i.e. not having the top and seat stained). But that’s another project for another post.